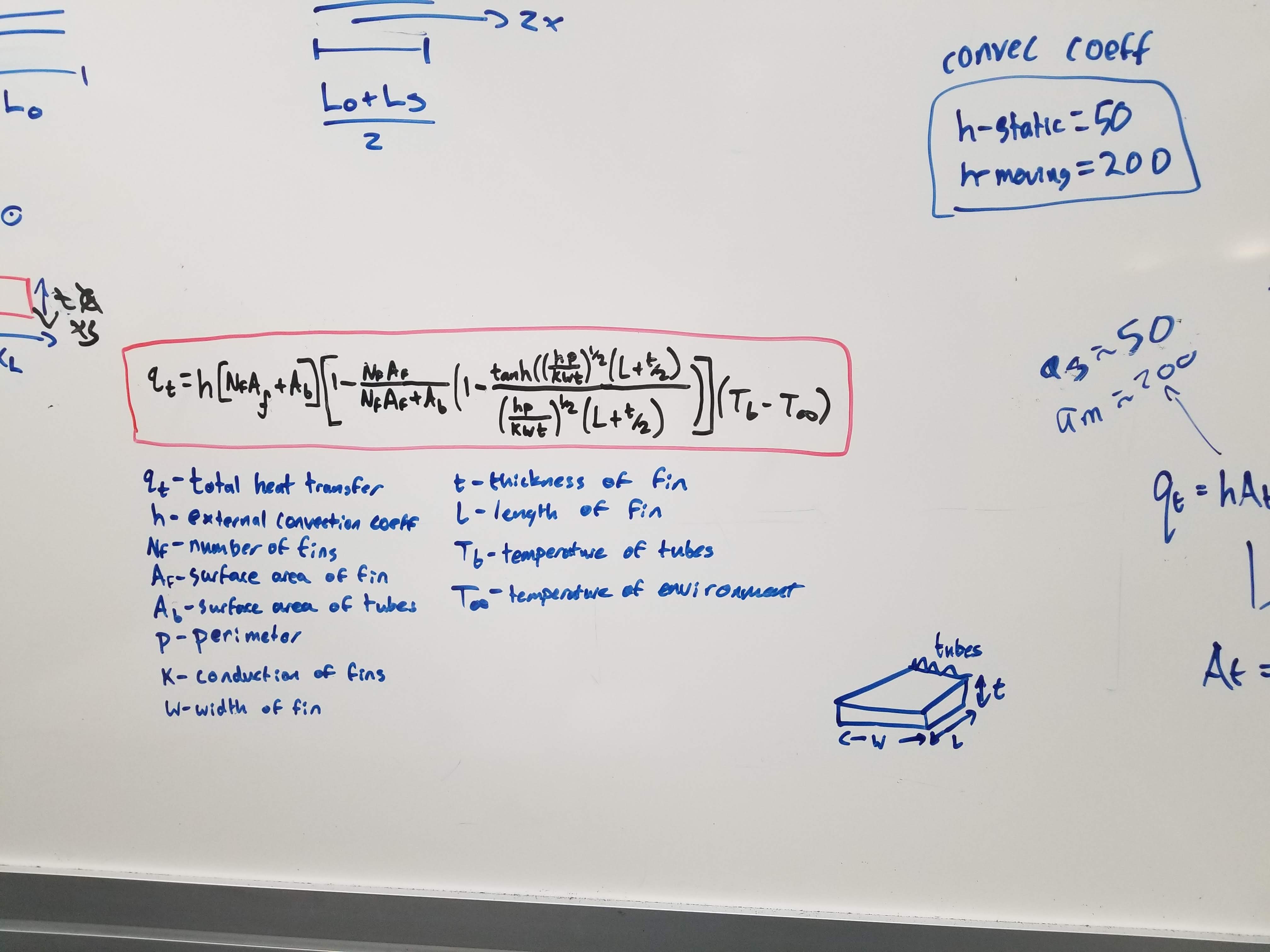
Design Process
This section will discuss the team’s approach to designing the Cerebro system, and discuss the layout prototypes created for this project.
Design Cycles
The team decided to have three design cycles, each with one-week iterations. Each design cycle had the team split into two, so each design challenge had a week to be focused on. Another bonus of this system was that each team member got time to work one on one with every team member. Each design challenge had a group focus on solutions for a week, starting with researching existing solutions, compiling all possible solutions, then structuring a chosen solution to work within the design parameters. At each design iteration’s conclusion groups would present their findings and proposal to the remaining team members and the project sponsor and advisor Dr. Joshua Gess for a full team discussion and the finalization of what proposal would be moved forward with.
In the first design iteration, Brodish and Bailey teamed up and focused on cooling applications of the hat. In week 3 of the project, the sub-team researched multiple cooling methods that could be implemented onto the hard hat. For a compressor, the team initially ideated various cooling methods that used air as the working fluid. The first concept had the compressor oriented towards the back end of the hat for convenience and weight distribution. This concept would allow the compressor to draw air in, then have the air compressed, filtered, and then finally be applied to the user. More research was conducted, and the sub-team came across an air cooler that uses vortex separation of air, to separate hot and cold air from a compressor that could then be filtered and applied to the user [1]. The vortex cooler called Vortec can be seen in Figure 1. However, when the team presented this idea to the client, he desired the main cooling methodology of the system to be the vapor compression cycle with refrigerant 134a as the coolant fluid. Refrigerant 134a is easily accessible, relatively cheap, and it has a low boiling point, which is needed for ensuring the fluid is a vapor when entering the compressor. The other sub-team group, Bergquist and Wise, focused on power supply possibilities and concluded that the best solution was a backpack containing a rechargeable 24-volt battery. This is because the compressor has a 24-volt requirement and could be used to attain one to two hours of usage at a time. The backpack is needed because the battery would not fit on the hat.
Figure 1: Vortec air cooler. Enclosure Climate Control.
Figure 2: Wise’s heat exchanger design.
Figure 3, 4: CAD Model of the Initial Prototype Condenser and Evaporator
Initial Layout Prototypes
This team focused on two iterative prototypes. The goals of these prototypes were to frame and shape components across the form of the hat, and to aid in visualizing what final tubing would look like to and from each component.
First iterations for the design focused on three main objectives. The first objective of this prototype was to create pathways for tubing from each of the four components. The team had an idea of what the overall shape of each component would look like and implemented their basic geometry during the prototype construction. Figures 2 and 3 demonstrate initial attempts to configure designs around the shape of a traditional hard hat. Through this initial prototype, tubing and weight distribution became important factors to consider moving forward with a second iteration. Tight fitting between components pictured in the figures below would be difficult to implement with less flexible metal tubing. This prototype was also very rear-loaded, requiring further improvements to component positioning.
Figure 5: First constructed prototype. Side and rear view respectively Figure 6: Side view of second prototype
The primary takeaway from the second prototype was the need to adjust the shape of the condenser. The condenser was arced originally to fit on a standard shaped hardhat, but the team decided to move forward with a cowboy hard hat due to the added mounting area around the brim of the hat. The condenser in all further iterations follows the shape of the top of the cowboy hat, which is discussed in the system section.